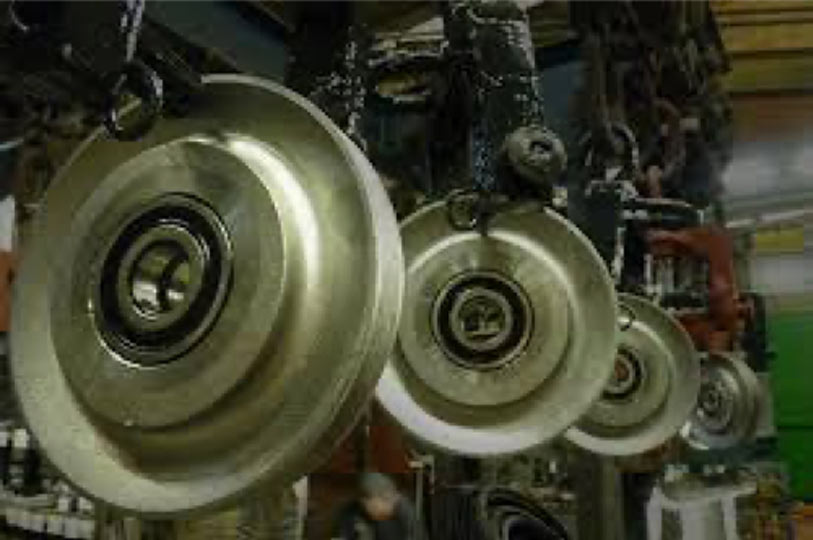
- Duration: 2 months
- Year: 2020
- Participants: GOSAM + SOMORROSTRO
- Industry 4.0 and advanced manufacturing
Project objectives
One of the stages of the pulley manufacturing process carried out by the company Gosan, consists of the union by welding the pulley throat, which is subsequently machined. The welding stage, which is done manually, causes the sizzle of material and sometimes part of that material is deposited inside the soul.
This metal chip of small dimensions causes that, during the start-up at the customer, and during the beginning of the pulley movement, this detached material hits against the core. The noise it causes is mistaken for the noise characteristic of a bearing in poor condition and the consequence is the rejection of the manufactured unit, reducing production efficiency.
The company does not know how to detect the noise caused by these shavings, so Somorrostro cooperates with the company.
Tasks performed
- Perform a technological check with the aim of being able to detect the manufacturing defect during the manufacturing process. For this, several technological alternatives are presented to be able to detect the chip inside the soul.
- Present different alternatives to the company:
- Ultrasonic technologies, which are used in existing failures in rolling equipment that rotate at speeds below 300 rpm.
- Vibration technologies, which are used in existing faults in rolling equipment that rotate at speeds above 300 rpm.
- Audio analysis technologies based on acoustic pattern recognition
- Advise on the choice of the best technology with the vision of ad-hoc subsequent development to automate the early detection of such anomaly during the manufacturing process prior to mechanization.
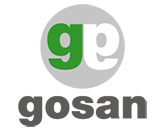
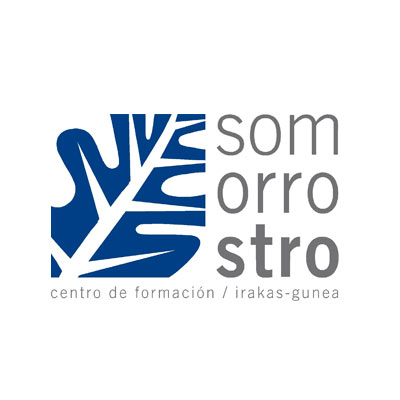